Several defects of welding
01. Undercut
If the welding process parameters are incorrectly selected or the operation is not standard, the grooves or depressions formed along the base metal during welding are called undercuts.
When you first start welding, because you don't know the magnitude of the current and your hands are unstable during welding, it's easy to cause undercuts. To prevent undercuts, you need to practice more welding techniques. You must be steady and don't be impatient.
Xinfa welding equipment has the characteristics of high quality and low price. For details, please visit: Welding & Cutting Manufacturers - China Welding & Cutting Factory & Suppliers (xinfatools.com)
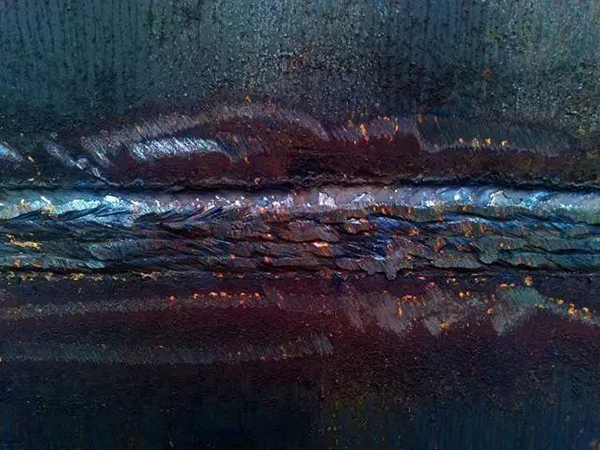
This is the photo of the undercut
02. Stomata
During welding, the gas in the molten pool fails to escape during solidification, and the cavities formed by remaining in the weld are called pores.
At the beginning of welding, due to the inability to master the welding rhythm and the unskilled way of transporting the strips, it will cause pauses, deeper and shallower, which can easily cause pores. The way to prevent it is not to be impatient when welding, grasp your own position, and carry out the strips step by step. In fact, it is the same as writing calligraphy. , just like writing, stroke by stroke.
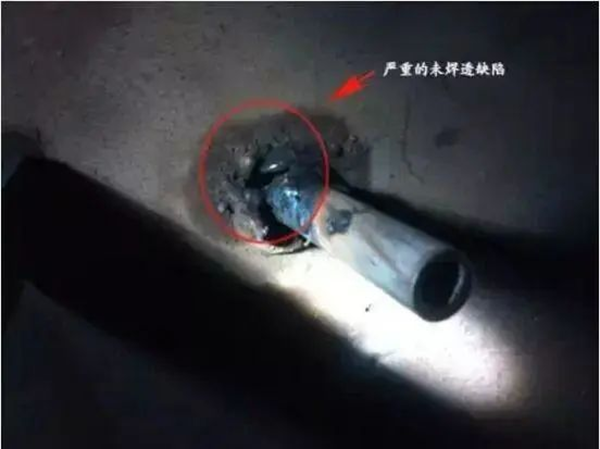
This is the welding hole
03. Not penetrated, not fused
There are many reasons for incomplete welding and incomplete fusion, such as: the gap or groove angle of the weldment is too small, the blunt edge is too thick, the diameter of the welding rod is too large, the welding speed is too fast or the arc is too long, etc. The welding effect may also be affected by the presence of impurities in the groove, and unmelted impurities may also affect the fusion effect of the weld.
Only when welding, control the welding speed, current and other process parameters, correctly select the groove size, and remove the oxide scale and impurities on the surface of the groove; the bottom welding must be thorough.
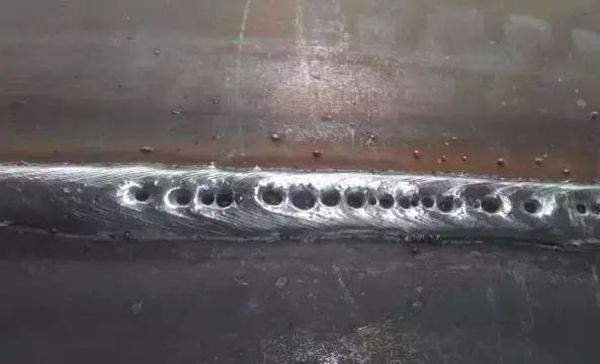
Not penetrated
04. Burn through
During the welding process, the molten metal flows out from the back of the groove, forming a perforated defect called burn-through.
The way to prevent it is to reduce the current and reduce the weld gap.
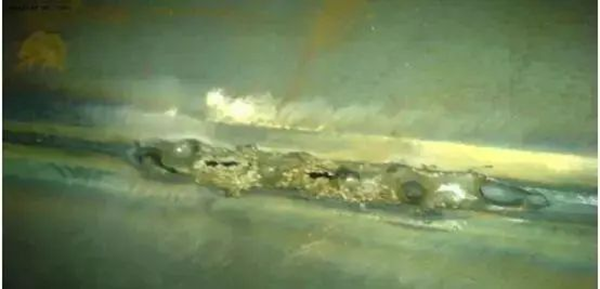
Welding pictures burn through
05. The welding surface is not beautiful
For example, defects such as overlap and serpentine weld beads are caused by the welding speed being too slow and the welding current being too low.
The way to prevent it is to practice more and master the appropriate welding speed. Most people do this in the beginning, practice more.
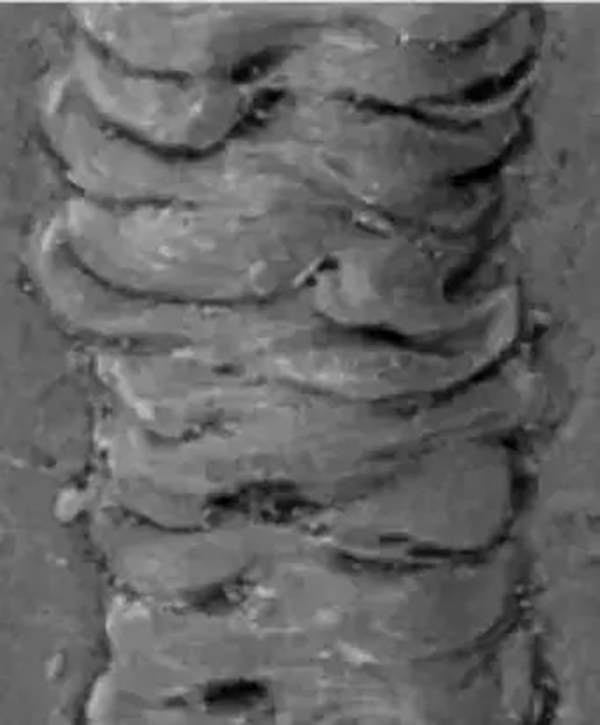
Serpentine weld bead
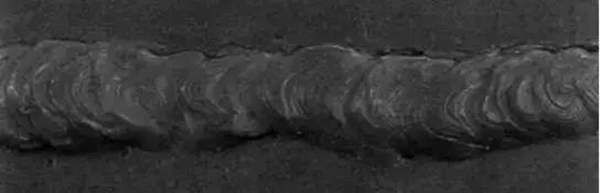
overlap weld
Post time: Dec-19-2023