1.The selection process of milling cutters generally consider the following aspects to choose:
(1) Part shape (considering the processing profile): The processing profile can generally be flat, deep, cavity, thread, etc. The tools used for different processing profiles are different. For example, a fillet milling cutter can mill convex surfaces, but not Milling concave surfaces.
(2) Material: Consider its machinability, chip forming, hardness and alloying elements. Tool manufacturers generally divide materials into steel, stainless steel, cast iron, non-ferrous metals, super alloys, titanium alloys and hard materials.
(3) Machining conditions: Machining conditions include the stability of the workpiece system of the machine tool fixture, the clamping situation of the tool holder and so on.
(4) Machine tool-fixture-workpiece system stability: This requires understanding the available power of the machine tool, spindle type and specifications, the age of the machine tool, etc., and the long overhang of the tool holder and its axial/radial runout Situation.
(5) Processing category and sub-category: This includes shoulder milling, plane milling, profile milling, etc., which need to be combined with the characteristics of the tool for tool selection.
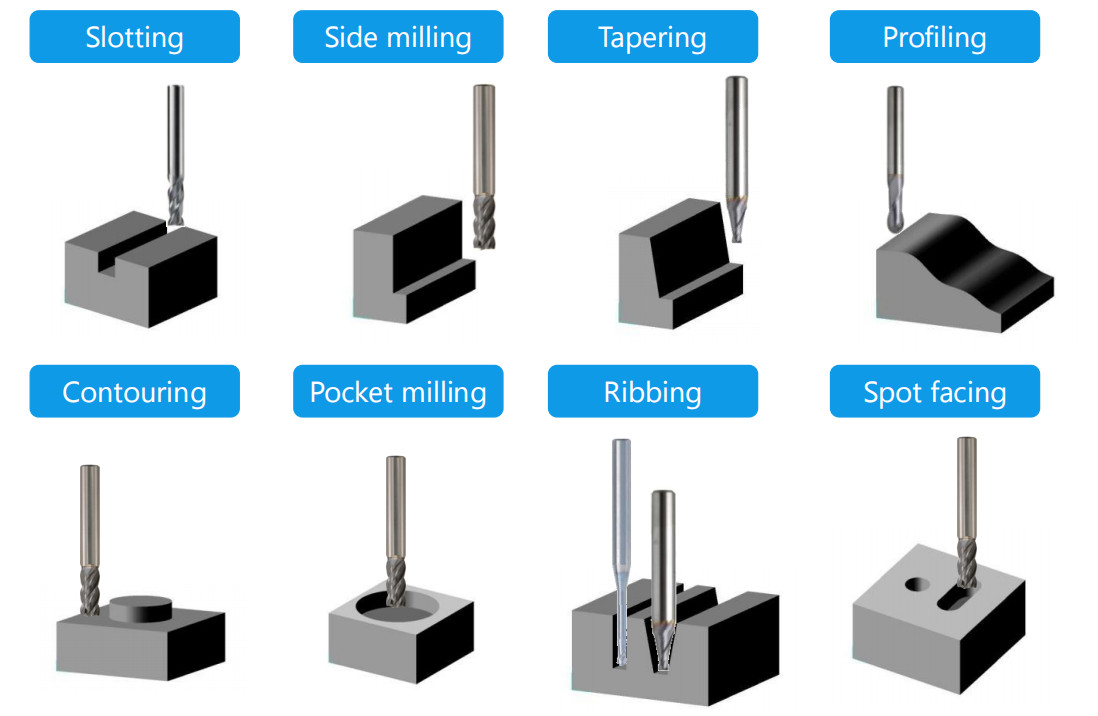
2. Selection of the geometric angle of the milling cutter
(1)The choice of front angle. The rake angle of the milling cutter should be determined according to the material of the tool and the workpiece. There are often impacts in milling, so it is necessary to ensure that the cutting edge has a higher strength. In general, the rake angle of a milling cutter is smaller than the cutting rake angle of a turning tool; high-speed steel is larger than a cemented carbide tool; in addition, when milling plastic materials, due to the larger cutting deformation, a larger rake angle should be used; when milling brittle materials , The rake angle should be smaller; when processing materials with high strength and hardness, a negative rake angle can also be used.
(2)Choice of blade inclination. The helix angle β of the outer circle of the end mill and the cylindrical milling cutter is the blade inclination λ s. This enables the cutter teeth to gradually cut in and out of the workpiece, improving the smoothness of milling. Increasing β can increase the actual rake angle, sharpen the cutting edge, and make chips easier to discharge. For milling cutters with narrow milling width, increasing the helix angle β is of little significance, so β=0 or a smaller value is generally taken.
(3)The choice of the main deflection angle and the secondary deflection angle. The effect of the entering angle of the face milling cutter and its influence on the milling process is the same as that of the entering angle of the turning tool in turning. The commonly used entering angles are 45°, 60°, 75°, and 90°. The rigidity of the process system is good, and the smaller value is used; otherwise, the larger value is used, and the entering angle selection is shown in Table 4-3. The secondary deflection angle is generally 5°~10°. The cylindrical milling cutter has only the main cutting edge and no secondary cutting edge, so there is no secondary deflection angle, and the entering angle is 90°.
Post time: Apr-17-2018