First of all, surface finish and surface roughness are the same concept, and surface finish is another name for surface roughness. Surface finish is proposed according to the visual point of view of people, while surface roughness is proposed according to the actual microscopic geometry of the surface. Because of the connection with the international standard (ISO), China adopted surface roughness and abolished surface finish after the 1980s. After the promulgation of the national standards for surface roughness GB3505-83 and GB1031-83, surface finish is no longer used.
There is a corresponding comparison table for surface finish and surface roughness. Roughness has a measurement calculation formula, while smoothness can only be compared with a sample gauge. Therefore, roughness is more scientific and rigorous than smoothness.
Surface glossiness indicates the intensity of diffuse reflection of light on the surface of an object. To the naked eye, if the surface diffuse reflection is strong, it is closer to the mirror effect, and the glossiness is high. On the contrary, if the surface diffuse reflection is weak, the glossiness is low, so the glossiness is also called mirror glossiness. The factors affecting surface gloss are related to the physical properties of the surface and the chemical properties of the materials used on the surface. The method of detecting the mirror gloss of the surface of an object requires the use of a surface gloss meter.
Surface roughness refers to the unevenness of the small spacing and tiny peaks and valleys on the processed surface. The distance (wave distance) between the two peaks or two valleys is very small (less than 1mm), which belongs to the microscopic geometric shape error. The smaller the surface roughness, the smoother the surface.
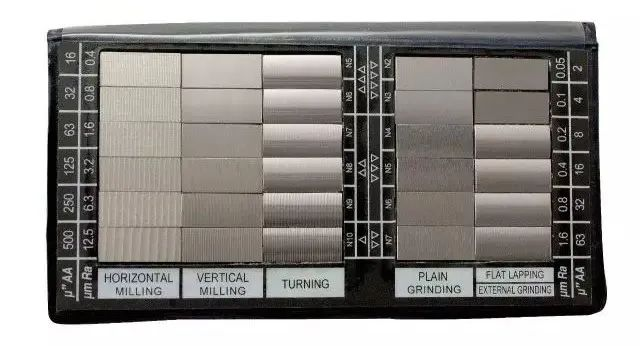
Surface roughness is generally formed by the processing method used and other factors, such as the friction between the tool and the surface of the part during processing, the plastic deformation of the surface metal during chip separation, and the high-frequency vibration in the process system. Due to the differences in processing methods and workpiece materials, the depth, density, shape and texture of the marks left on the processed surface are different.
Surface roughness is closely related to the matching properties, wear resistance, fatigue strength, contact stiffness, vibration and noise of mechanical parts, and has an important impact on the service life and reliability of mechanical products. Ra is generally used for marking.
The influence of surface roughness on parts is mainly manifested in the following aspects: The rougher the surface, the smaller the effective contact area between the matching surfaces, the greater the pressure, the greater the friction resistance, and the faster the wear.
Xinfa CNC tools have the characteristics of good quality and low price. For details, please visit: CNC Tools Manufacturers - China CNC Tools Factory & Suppliers (xinfatools.com)
The influence on the stability of the fit For clearance fit, the rougher the surface, the easier it is to wear, causing the gap to gradually increase during the working process; for interference fit, since the microscopic convex peaks are squeezed flat during assembly, the actual effective interference is reduced, and the connection strength is reduced.
Affecting fatigue strength Rough parts have large troughs on their surfaces, which are sensitive to stress concentration like sharp notches and cracks, thus affecting the fatigue strength of the parts.
Affecting corrosion resistance Rough parts make it easy for corrosive gases or liquids to penetrate into the inner layer of the metal through the microscopic valleys on the surface, causing surface corrosion.
Affecting sealing Rough surfaces cannot fit tightly together, and gases or liquids leak through the gaps between the contact surfaces.
Affecting contact stiffness Contact stiffness is the ability of the joint surface of a part to resist contact deformation under the action of external forces. The stiffness of the machine depends to a large extent on the contact stiffness between the parts.
Affecting measurement accuracy The surface roughness of the measured surface of the part and the measuring surface of the measuring tool will directly affect the measurement accuracy, especially in precision measurement.
In addition, surface roughness will have varying degrees of influence on the coating, thermal conductivity and contact resistance, reflection ability and radiation performance of the part, resistance to the flow of liquids and gases, and the flow of current on the surface of the conductor.
Post time: Sep-03-2024