Alloy tool materials are made of carbide (called hard phase) and metal (called binder phase) with high hardness and melting point through powder metallurgy. Wherein the alloy carbide tool materials commonly used have WC, TiC, TaC, NbC, etc., commonly used binders are Co, titanium carbide-based binder is Mo, Ni.
The physical and mechanical properties of alloy tool materials depend on the composition of the alloy, the thickness of the powder particles and the sintering process of the alloy. The more hard phases with high hardness and high melting point, the higher the hardness and high temperature hardness of the alloy tool The more the binder, the higher the strength. The addition of TaC and NbC to the alloy is beneficial to refine the grains and improve the heat resistance of the alloy. The commonly used cemented carbide contains a large amount of WC and TiC, so the hardness, wear resistance and resistance The heat resistance is higher than that of tool steel, the hardness at room temperature is 89~94HRA, and the heat resistance is 80~1000 degrees.
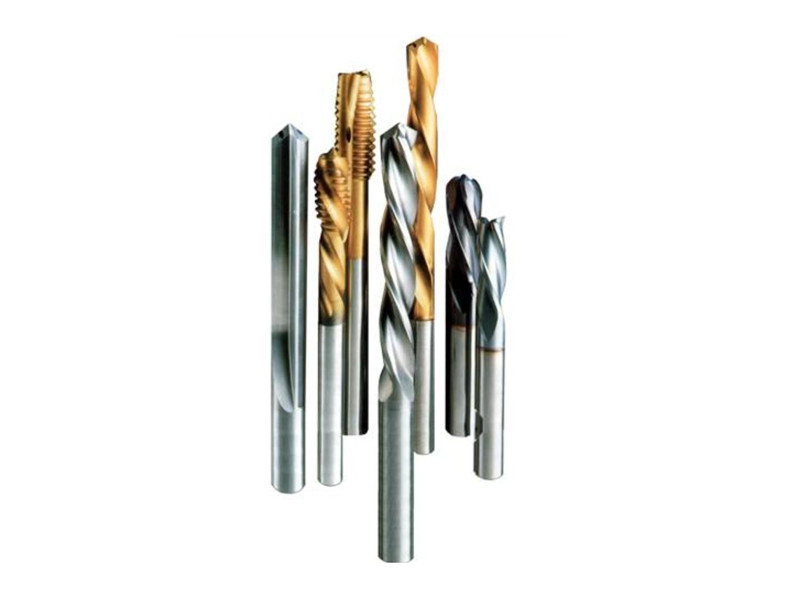
Post time: May-22-2017