Dissimilar metals refer to metals of different elements (such as aluminum, copper, etc.) or certain alloys formed from the same basic metal (such as carbon steel, stainless steel, etc.) that have significant differences in metallurgical properties, such as physical properties, chemical properties, etc. They can be used as base metal, filler metal or weld metal.
Welding of dissimilar materials refers to the process of welding two or more different materials (referring to different chemical compositions, metallographic structures, properties, etc.) under certain process conditions. Among the welding of dissimilar metals, the most common is the welding of dissimilar steel, followed by the welding of dissimilar non-ferrous metals and the welding of steel and non-ferrous metals.
From the perspective of joint forms, there are three basic situations, namely joints with two different metal base materials, joints with the same base metal but different filler metals (such as joints using austenitic welding materials to weld medium-carbon quenched and tempered steel, etc.), And welded joints of composite metal plates, etc.
The welding of dissimilar materials is when two different metals are welded together, a transition layer with different properties and structure from the base metal will inevitably be produced. Because dissimilar metals have significant differences in elemental properties, physical properties, chemical properties, etc., compared with the welding of the same material, the welding of dissimilar materials is much more complex in terms of welding mechanism and operating technology. .
Xinfa welding equipment has the characteristics of high quality and low price. For details, please visit: Welding & Cutting Manufacturers - China Welding & Cutting Factory & Suppliers (xinfatools.com)
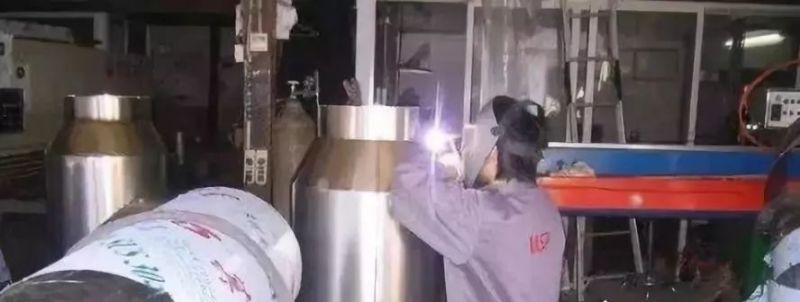
The main problems existing in the welding of dissimilar materials are as follows:
1. The greater the difference in melting points of dissimilar materials, the more difficult it is to weld.
This is because when the material with a low melting point reaches the molten state, the material with a high melting point is still in a solid state. At this time, the melted material easily penetrates into the grain boundaries of the superheated zone, causing the loss of the low melting point material and the burning or evaporation of the alloy elements. Make welding joints difficult to weld. For example, when welding iron and lead (which have very different melting points), not only do the two materials not dissolve each other in the solid state, but they also cannot dissolve each other in the liquid state. The liquid metal is distributed in layers and crystallizes separately after cooling.
2. The greater the difference in linear expansion coefficients of dissimilar materials, the more difficult it is to weld.
Materials with larger linear expansion coefficients will have larger thermal expansion rates and greater shrinkage during cooling, which will produce large welding stress when the molten pool crystallizes. This welding stress is not easy to eliminate, resulting in large welding deformation. Due to the different stress states of the materials on both sides of the weld, it is easy to cause cracks in the weld and the heat-affected zone, and even cause the weld metal to peel off the base metal.
3. The greater the difference in thermal conductivity and specific heat capacity of dissimilar materials, the more difficult it is to weld.
The thermal conductivity and specific heat capacity of the material will deteriorate the crystallization conditions of the weld metal, seriously coarsen the grains, and affect the wetting performance of the refractory metal. Therefore, a powerful heat source should be used for welding. During welding, the position of the heat source should be toward the side of the base metal with good thermal conductivity.
4. The greater the electromagnetic difference between dissimilar materials, the more difficult it is to weld.
Because the greater the electromagnetic difference between materials, the more unstable the welding arc will be and the worse the weld will be.
5. The more intermetallic compounds formed between dissimilar materials, the more difficult it is to weld.
Because intermetallic compounds are relatively brittle, they can easily cause cracks or even breakage in the weld.
6. During the welding process of dissimilar materials, due to changes in the metallographic structure of the welding area or newly formed structures, the performance of the welded joints deteriorates, which brings great difficulties to the welding.
The mechanical properties of the joint fusion zone and heat-affected zone are poor, especially the plastic toughness is significantly reduced. Due to the decrease in plastic toughness of the joint and the existence of welding stress, welded joints of dissimilar materials are prone to cracks, especially in the welding heat-affected zone, which is more likely to crack or even break.
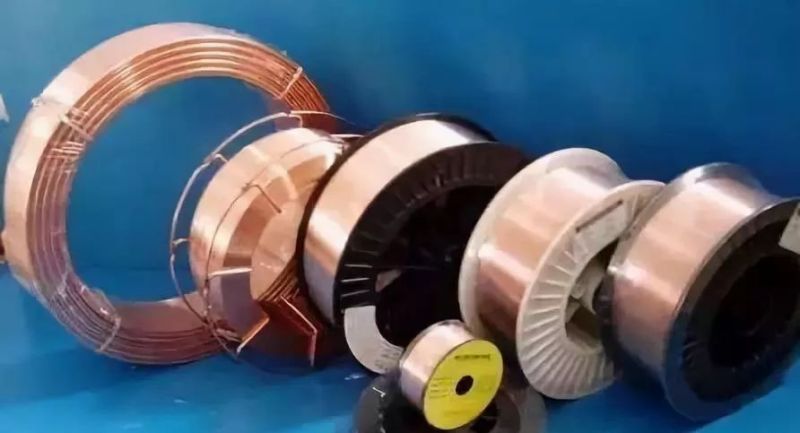
7. The stronger the oxidation of dissimilar materials, the more difficult it is to weld.
For example, when copper and aluminum are welded by fusion welding, copper and aluminum oxides are easily formed in the molten pool. During cooling and crystallization, the oxides present at the grain boundaries can reduce the intergranular bonding force.
8. When welding dissimilar materials, it is difficult for the welding seam and the two base metals to meet the requirements of equal strength.
This is because metal elements with low melting points are easy to burn and evaporate during welding, which changes the chemical composition of the weld and reduces its mechanical properties, especially when welding dissimilar non-ferrous metals.
Post time: Dec-28-2023