With the progress of science and technology and the development of economy, the application scope of nitrogen is expanding day by day, and has penetrated into many industrial sectors and daily life.
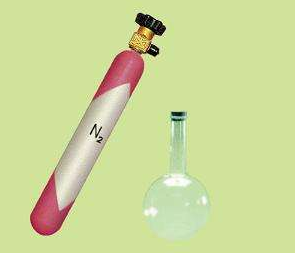
Nitrogen Production Manufacturers - China Nitrogen Production Factory & Suppliers (xinfatools.com)
Nitrogen is the main component of air, accounting for about 78% of air. Elemental nitrogen N2 is a colorless and odorless gas under normal conditions. The gas density under standard state is 1.25 g/L. The melting point is -210℃ and the boiling point is -196℃. Liquid nitrogen is a low-temperature refrigerant (-196℃).
Today we will introduce several main methods for producing nitrogen at home and abroad.
There are three general industrial-scale nitrogen production methods: cryogenic air separation nitrogen production, pressure swing adsorption nitrogen production, and membrane separation nitrogen production.
First: Cryogenic air separation nitrogen production method
Cryogenic air separation nitrogen production is a traditional nitrogen production method with a history of nearly several decades. It uses air as raw material, compresses and purifies it, and then uses heat exchange to liquefy the air into liquid air. Liquid air is mainly a mixture of liquid oxygen and liquid nitrogen. The different boiling points of liquid oxygen and liquid nitrogen are used to separate them through the distillation of liquid air to obtain nitrogen.
Advantages: large gas production and high purity of product nitrogen. Cryogenic nitrogen production can produce not only nitrogen but also liquid nitrogen, which meets the process requirements of liquid nitrogen and can be stored in liquid nitrogen storage tanks. When there is an intermittent nitrogen load or a minor repair of the air separation equipment, the liquid nitrogen in the storage tank enters the vaporizer and is heated, and then sent to the product nitrogen pipeline to meet the nitrogen demand of the process unit. The operating cycle of cryogenic nitrogen production (referring to the interval between two large heatings) is generally more than 1 year, so cryogenic nitrogen production is generally not considered as a standby.
Disadvantages: Cryogenic nitrogen production can produce nitrogen with a purity of ≧99.999%, but the purity of nitrogen is limited by nitrogen load, number of trays, tray efficiency and oxygen purity in liquid air, and the adjustment range is very small. Therefore, for a set of cryogenic nitrogen production equipment, the product purity is basically certain and inconvenient to adjust. Since the cryogenic method is carried out at extremely low temperatures, the equipment must have a pre-cooling start-up process before it is put into normal operation. The start-up time, that is, the time from the start of the expander to the time when the nitrogen purity reaches the requirement, is generally not less than 12 hours; before the equipment enters the overhaul, it must have a period of heating and thawing time, generally 24 hours. Therefore, the cryogenic nitrogen production equipment should not be started and stopped frequently, and it is advisable to operate continuously for a long time.
In addition, the cryogenic process is complex, occupies a large area, has high infrastructure costs, requires special maintenance forces, has a large number of operators, and produces gas slowly (18 to 24 hours). It is suitable for large-scale industrial nitrogen production.
Second: Pressure Swing Adsorption (PSA) Nitrogen Production Method
Pressure Swing Adsorption (PSA) gas separation technology is an important branch of non-cryogenic gas separation technology. It is the result of people's long-term efforts to find a simpler air separation method than the cryogenic method.
In the 1970s, the West German Essen Mining Company successfully developed carbon molecular sieves, paving the way for the industrialization of PSA air separation nitrogen production. Over the past 30 years, this technology has developed rapidly and matured. It has become a strong competitor of cryogenic air separation in the field of small and medium-sized nitrogen production.
Pressure swing adsorption nitrogen production uses air as raw material and carbon molecular sieve as adsorbent. It uses the characteristics of carbon molecular sieve's selective adsorption of oxygen and nitrogen in the air, and uses the principle of pressure swing adsorption (pressure adsorption, pressure reduction desorption and molecular sieve regeneration) to separate oxygen and nitrogen at room temperature to produce nitrogen.
Compared with cryogenic air separation nitrogen production, pressure swing adsorption nitrogen production has significant advantages: adsorption separation is carried out at room temperature, the process is simple, the equipment is compact, the footprint is small, it is easy to start and stop, it starts quickly, the gas production is fast (generally about 30 minutes), the energy consumption is small, the operating cost is low, the degree of automation is high, the operation and maintenance are convenient, the skid installation is convenient, no special foundation is required, the product nitrogen purity can be adjusted within a certain range, and the nitrogen production is ≤3000Nm3/h. Therefore, pressure swing adsorption nitrogen production is particularly suitable for intermittent operation.
However, so far, domestic and foreign counterparts can only produce nitrogen with a purity of 99.9% (i.e., O2≤0.1%) using PSA nitrogen production technology. Some companies can produce 99.99% pure nitrogen (O2≤0.01%). Higher purity is possible from the perspective of PSA nitrogen production technology, but the production cost is too high and users are unlikely to accept it. Therefore, the use of PSA nitrogen production technology to produce high-purity nitrogen must also add a post-stage purification device.
Nitrogen purification method (industrial scale)
(1) Hydrogenation deoxygenation method.
Under the action of a catalyst, the residual oxygen in the nitrogen reacts with the added hydrogen to produce water, and the reaction formula is: 2H2 + O2 = 2H2O. Then, the water is removed by a high-pressure nitrogen compressor booster, and the high-purity nitrogen with the following main components is obtained by post-drying: N2≥99.999%, O2≤5×10-6, H2≤1500×10-6, H2O≤10.7×10-6. The cost of nitrogen production is about 0.5 yuan/m3.
(2) Hydrogenation and deoxygenation method.
This method is divided into three stages: the first stage is hydrogenation and deoxygenation, the second stage is dehydrogenation, and the third stage is water removal. High-purity nitrogen with the following composition is obtained: N2 ≥ 99.999%, O2 ≤ 5 × 10-6, H2 ≤ 5 × 10-6, H2O ≤ 10.7 × 10-6. The cost of nitrogen production is about 0.6 yuan/m3.
(3) Carbon deoxygenation method.
Under the action of carbon-supported catalyst (at a certain temperature), the residual oxygen in ordinary nitrogen reacts with the carbon provided by the catalyst itself to generate CO2. Reaction formula: C + O2 = CO2. After the subsequent stage of removing CO2 and H2O, high-purity nitrogen with the following composition is obtained: N2 ≥ 99.999%, O2 ≤ 5 × 10-6, CO2 ≤ 5 × 10-6, H2O ≤ 10.7 × 10-6. The cost of nitrogen production is about 0.6 yuan/m3.
Third: Membrane separation and air separation nitrogen production
Membrane separation and air separation nitrogen production is also a new branch of non-cryogenic nitrogen production technology. It is a new nitrogen production method that developed rapidly abroad in the 1980s. It has been promoted and applied in China in recent years.
Membrane separation nitrogen production uses air as raw material. Under a certain pressure, it uses the different permeation rates of oxygen and nitrogen in the hollow fiber membrane to separate oxygen and nitrogen to produce nitrogen. Compared with the above two nitrogen production methods, it has the characteristics of simpler equipment structure, smaller volume, no switching valve, simpler operation and maintenance, faster gas production (within 3 minutes), and more convenient capacity expansion.
However, hollow fiber membranes have stricter requirements on the cleanliness of compressed air. The membranes are prone to aging and failure, and are difficult to repair. New membranes need to be replaced.
Membrane separation nitrogen production is more suitable for small and medium-sized users with nitrogen purity requirements of ≤98%, and has the best function-price ratio at this time; when the nitrogen purity is required to be higher than 98%, it is about 30% higher than the pressure swing adsorption nitrogen production device of the same specification. Therefore, when high-purity nitrogen is produced by combining membrane separation nitrogen production and nitrogen purification devices, the purity of general nitrogen is generally 98%, which will increase the production cost and operation cost of the purification device.
Post time: Jul-24-2024