Many newcomers will encounter that the company requires designers to go to the workshop for internship for a period of time before entering the office to design, and many newcomers don't want to go.
1. The workshop smells bad.
2. Some people say that I have learned it in college and I don't need to go.
3. The people in the workshop are like this and that (such as asking them to be younger brothers... I won't say more here).
So many people are unwilling to go, and even those who are willing to go are confused and don't know what to learn, because they think what learning has to do with design. Most designers design in the office, and they don't go to the workshop to work with the processing master. Here I want to say that your focus is wrong.
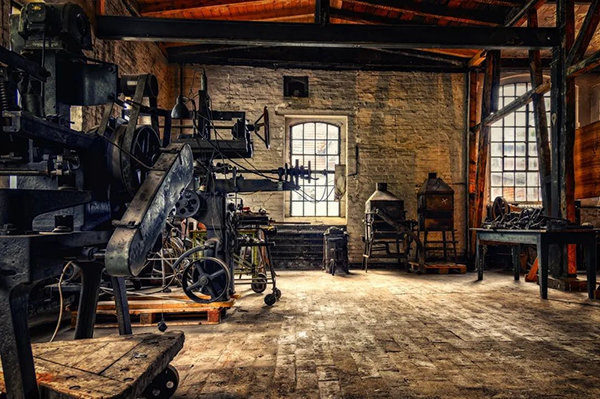
Correction:
1. Learn processing from the workshop master.
This will allow you to design fewer scrap parts in the future. Many newcomers think that everything drawn by SW can be processed. Here I want to say that I used to work in a small company. Once the designer designed a 90° hook (that is, a small iron sheet of -6×20×100 was bent into 90°) and opened a 6mm diameter hole 8mm away from the corner.
This is a problem. Of course, it can be drawn, but the factory conditions cannot make it. The reason is that if the hole is opened first and then folded, the hole becomes an ellipse. If the corner is folded first and then the hole is opened, it is difficult to clamp. If it is too hard, the parts will be scrapped. If it is not enough, the parts will also be scrapped, and there will be injuries.
2. Learn the processing process of parts in the workshop.
The part processing process mentioned here is the processing in your mind. Many old engineers have the whole part processing process in their heads when designing, and then draw the parts, and require the parts to be processed easily. It is best if it can be completed in one cut. Of course, this requires hard work.
When you design, you think of yourself as the worker who is going to process this part at that time. How can you complete the processing of this part and how can you meet the processing requirements of the part? Think about it, then draw this part. When you achieve this, I believe that the master can also understand the drawings you draw.
Xinfa CNC tools have the characteristics of good quality and low price. For details, please visit: CNC Tools Manufacturers - China CNC Tools Factory & Suppliers (xinfatools.com)
3. Learn to assemble in the workshop
Some companies may only make parts but not assemble them. I am just talking about my personal opinion here, and you can also take a look. Many newcomers don’t understand why verticality should be added here, coaxiality should be added there, and parallelism should be added there...especially roughness. I believe many people will ask!
In fact, most of these are assembly and operation issues, of course there are others (such as roughness, some are for the feel, I won’t say more here).
In the workshop, assembly is also a science. Many workshop masters who engage in assembly will take a level to measure, based on the thermal stress of welding and the principle of the straight line of light to observe whether the requirements are met. In fact, these are all based on your design. Verticality requires that the equipment can be vertical during assembly. A small error will be infinitely expanded during operation and become an error. The same is true for coaxiality and parallelism.
Think more about what will happen to the geometric tolerances you marked during assembly and operation, and you will know the importance of geometric tolerances. For example, with coaxiality as the standard, the processing master processes according to the general situation, but the result is that it cannot be assembled, or it deviates up and down during operation. How can the accuracy of the equipment be guaranteed?
Supplement: Some processing masters have some deviations in their methods. I once worked in a Taiwanese company. At that time, the company accepted senior interns. One intern found that the factory master’s hole-drilling method was wrong and could not meet the requirements of the parts. He created a new hole-drilling method based on his own hole-drilling experience and book knowledge.
I hope it will be helpful to those who are just getting started.
Post time: Aug-26-2024