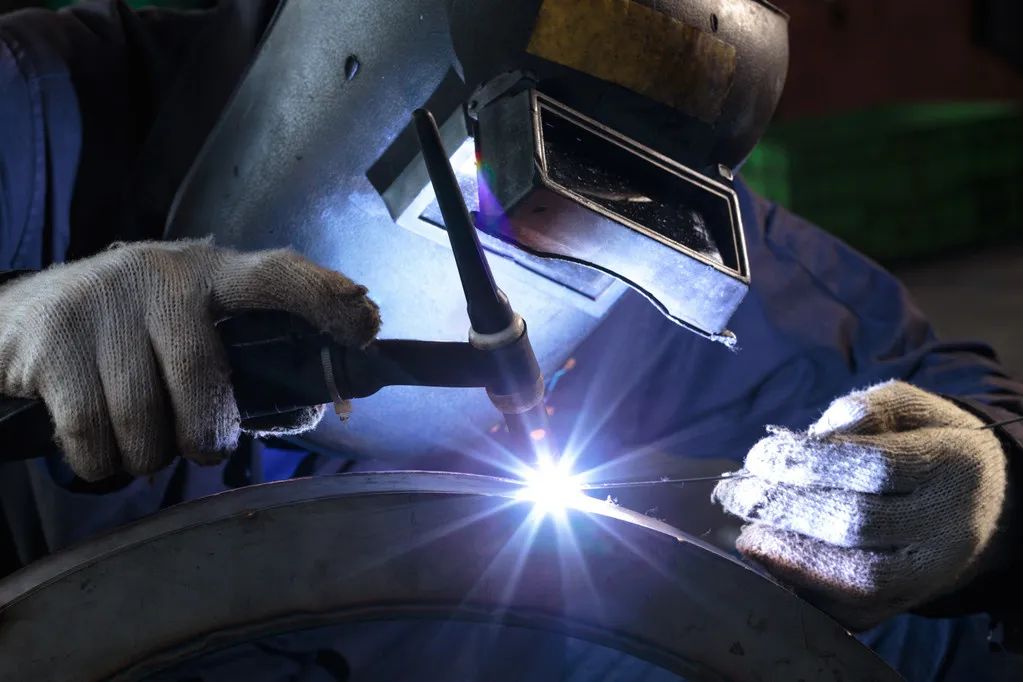
1 Overview
Large container ships have characteristics such as large length, container capacity, high speed, and large openings, resulting in a high stress level in the middle area of the hull structure. Therefore, large-thickness high-strength steel materials are often used in design.
As a high-efficiency welding method, single-wire electric gas vertical welding (EGW) is widely used. However, generally the maximum applicable plate thickness can only reach 32~33mm, and cannot be used on the above-mentioned large thick plates;
The applicable plate thickness of the double-wire EGW method is generally up to about 70mm. However, because the welding heat input is very large, to ensure that the performance of the welded joint meets the specification requirements, a steel plate that is suitable for high heat input welding must be used.
Therefore, without using welded steel plates that can adapt to large heat input, the vertical butt welding of large and thick plates can only use FCAW multi-layer multi-pass welding, and the welding efficiency is low.
This method is a FCAW+EGW combined welding process method developed based on the above characteristics that can not only apply EGW to the welding of large thick plates, give full play to its high efficiency advantages, but also adapt to the characteristics of actual steel plates. That is, an efficient combined welding method that uses FCAW single-sided welding on the structural surface to achieve backside forming, and then performs EGW welding on the non-structural surface.
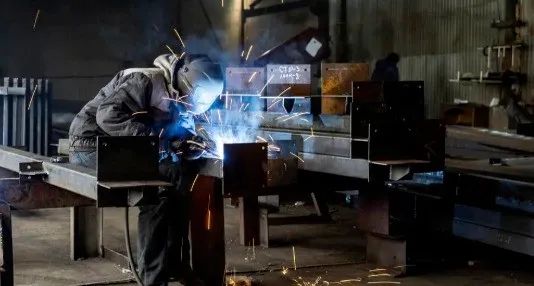
Xinfa welding equipment has the characteristics of high quality and low price. For details, please visit: Welding & Cutting Manufacturers - China Welding & Cutting Factory & Suppliers (xinfatools.com)
2 Key points of FCAW+EGW combined welding method
(1) Applicable plate thickness
34~80mm: That is, the lower limit is the upper limit of the applicable plate thickness for monofilament EGW; as for the upper limit, currently a large container ship uses large-thickness steel plates for the inner side and upper shell strake plates. Considering that the thickness of the steel plates of different products is different, it is determined to be 80mm.
(2) Thickness division
The principle of dividing welding thickness is to give full play to the high efficiency advantage of EGW welding; at the same time, we must take into account that the amount of welding deposited metal between the two methods must not differ too much, otherwise it will be difficult to control the welding deformation.
(3) Combined welding method joint form design
① Groove angle: In order to avoid the groove width being too large on the FCAW side, the groove is appropriately smaller than the normal FCAW single-sided welding groove, which is Different plate thicknesses require different bevel angles. When the plate thickness is 30~50mm, it is Y±5°, and when the plate thickness is 51~80mm, it is Z±5°.
② Root gap: It needs to adapt to the process requirements of both welding methods at the same time, that is, G±2mm.
③Applicable gasket form: Conventional triangular gaskets cannot meet the above joint form requirements due to angle problems. This combined welding method requires the use of round bar gaskets. The diameter size needs to be selected based on the actual assembly gap value (see Figure 1).
(4) Basic points of welding construction
①Welding training. Operators need to undergo a certain period of training. Even operators with experience in EGW (SG-2 method) welding of ordinary thickness steel plates must undergo training, because the operating movements of the welding wire in the molten pool are different when welding thin plates and large thick plates.
②End detection. Non-destructive testing (RT or UT) must be used at the end of the weld and the arc stop part to check for defects and confirm the size of the defects. Gouging is used to remove defects, and FCAW or SMAW welding methods are used for rework welding.
③Arc striking plate. The arc striking plate length must be at least 50mm. The arc striking plate and the base material have the same thickness and have the same groove. ④ During welding, wind will cause disorder of the shielding gas, causing pore defects in the weld, and the intrusion of nitrogen in the air will cause poor joint performance, so necessary wind protection measures need to be taken.
3 Process testing and approval
(1) Test materials
The test plates and welding materials are shown in Table 1
(2) Welding parameters
The welding position is 3G, and the specific welding parameters are shown in Table 2.
(3) Test results
The test was conducted in accordance with LR and CCS ship regulations and under on-site supervision by the surveyor. The results are as follows.
NDT and results: PT results are that the edges of the front and back welds are neat, the surface is smooth, and there are no surface defects; UT results are that all welds are qualified after ultrasonic testing (meeting ISO 5817 level B); MT results are that the front and back welds are magnetic particle flaw detection After inspection, there were no surface welding defects.
(4) Accept the conclusion
After NDT and mechanical properties testing were conducted on the test welded joints, the results met the requirements of the classification society's specifications and passed the process approval.
(5) Efficiency comparison
Taking a 1m long weld of a certain plate as an example, the welding time required for double-sided FCAW welding is 250 minutes; when the combined welding method is used, the welding time required for EGW is 18 minutes, and the welding time required for FCAW is 125 minutes, and the total welding time is 143 minutes. The combined welding method saves nearly 43% of the welding time compared to the original double-sided FCAW welding.
4 Conclusion
The FCAW+EGW combined welding method developed experimentally not only takes full advantage of the high efficiency of EGW welding, but also adapts to the current characteristics of steel plates. It is a new welding process technology with high welding efficiency and high feasibility.
As an innovative welding process technology, its groove production, assembly accuracy, material selection, welding parameters, etc. are crucial and must be strictly controlled during implementation.
Post time: Feb-22-2024