Coated carbide tools have the following advantages:
(1) The coating material of the surface layer has extremely high hardness and wear resistance. Compared with the uncoated cemented carbide, the coated cemented carbide allows the use of higher cutting speeds, thereby improving the processing efficiency, or It can greatly increase the tool life at the same cutting speed.
(2) The coefficient of friction between the coated material and the processed material is small. Compared with the uncoated cemented carbide, the cutting force of the coated cemented carbide is reduced to a certain extent, and the processed surface quality is better.
(3) Due to the good comprehensive performance, the coated carbide knife has better versatility and wider application range. The most commonly used method of cemented carbide coating is high temperature chemical vapor deposition (HTCVD). Plasma chemical vapor deposition (PCVD) is used to coat the surface of cemented carbide.
Coating types of cemented carbide milling cutters:
The three most common coating materials are titanium nitride (TiN), titanium carbonitride (TiCN) and titanium aluminide (TiAIN).
Titanium nitride coating can increase the hardness and wear resistance of the tool surface, reduce the friction coefficient, reduce the generation of built-up edge, and extend the life of the tool. Titanium nitride coated tools are suitable for processing low-alloy steel and stainless steel.
The surface of the titanium carbonitride coating is gray, the hardness is higher than that of the titanium nitride coating, and the wear resistance is better. Compared with the titanium nitride coating, the titanium carbonitride coating tool can be processed at a greater feed speed and cutting speed (40% and 60% higher than that of the titanium nitride coating, respectively), and the workpiece material removal rate is higher. Titanium carbonitride coated tools can process a variety of workpiece materials.
The titanium aluminide coating is gray or black. It is mainly coated on the surface of the cemented carbide tool base. It can still be processed when the cutting temperature reaches 800 ℃. It is suitable for high-speed dry cutting. During dry cutting, the chips in the cutting area can be removed with compressed air. Titanium aluminide is suitable for processing brittle materials such as hardened steel, titanium alloy, nickel-based alloy, cast iron and high silicon aluminum alloy.
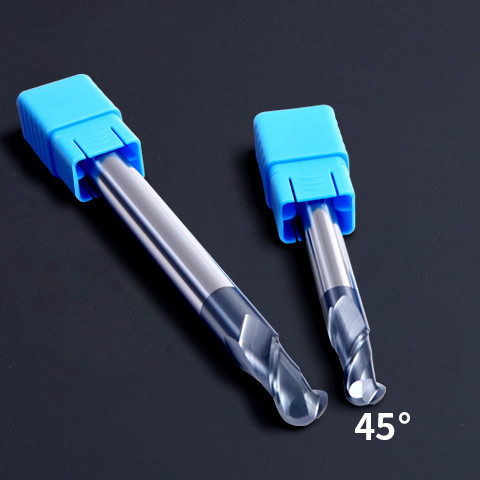
Coating application of cemented carbide milling cutter:
The progress of tool coating technology is also reflected in the practicality of nano-coating. Coating hundreds of layers of materials with a thickness of several nanometers on the tool base material is called nano-coating. The size of each particle of the nano-coating material is very small, so the grain boundary is very long, which has high high-temperature hardness. Strength and fracture toughness.
The Vickers hardness of the nano-coating can reach HV2800~3000, and the wear resistance is improved by 5%~50% than that of micron materials. According to reports, at present, 62 layers of coating tools with alternating coatings of titanium carbide and titanium carbonitride and 400 layers of TiAlN-TiAlN/Al2O3 nano-coated tools have been developed.
Compared with the above hard coatings, sulfide (MoS2, WS2) coated on high-speed steel is called soft coating, which is mainly used for cutting high-strength aluminum alloys, titanium alloys and some rare metals.
If you have any need, please come to contact XINFA, we delicate to offering standard size tools in a short time and customized tools plan for customers.
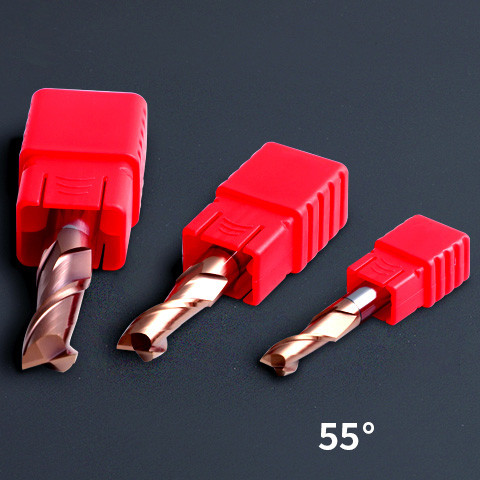
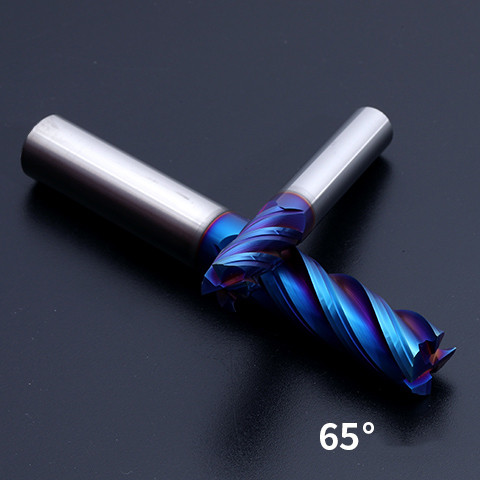
Post time: Aug-14-2015