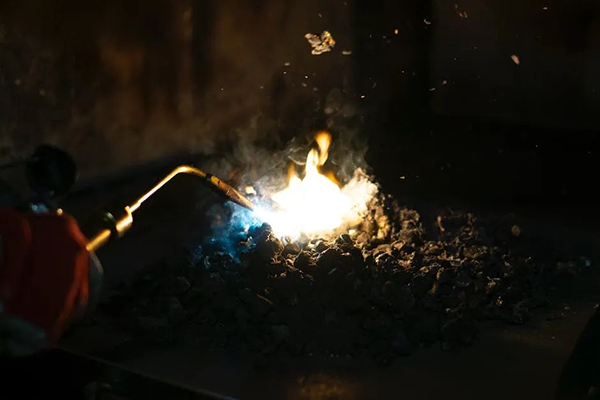
1. Background Abstract
The requirements for pipeline prefabrication in the offshore engineering and petrochemical industries are relatively high, and the amount of work is relatively large. The traditional TIG welding manual base and MIG welding filling and covering are used, but the quality and efficiency are not ideal. This paper adopts a new welding process-high-efficiency hot wire TIG welding, to achieve TIG base welding, filling welding and covering welding, and achieves MIG welding high-efficiency welding method to replace the traditional method. Through this experiment, the mechanical properties of the research have been proven to be effective and have been successfully used in the industry.
Research purpose
At present, the traditional welding process uses manual TIG welding for base, manual welding or MIG welding, submerged arc welding and other multi-process methods to fill and cover to improve welding efficiency. However, these filling and covering methods are not easy to achieve automatic welding, are not suitable for various pipe diameters, are relatively easy to produce welding defects, and the welding quality pass rate is limited by the workers' operating level.
Compared with ordinary TIG welding, hot wire TIG welding adds a separate hot wire power supply to preheat the welding wire on the basis of traditional cold wire, and increases the melting speed of the welding wire without changing the welding line energy. In this way, the welding arc provided only needs to spend a small amount of energy to melt the welding wire, thereby improving welding production efficiency.
High-efficiency hot wire TIG is more than 5 times more efficient than ordinary TIG, comparable to MIG welding speed, and the deposition rate is increased from 0.3~0.5kg/h to 2~4kg/h. Domestic hot wire TIG technology is in a stagnant stage and is far from achieving efficient and high-quality welding. The efficiency of foreign hot wire TIG welding process has not been significantly improved and cannot reach the efficiency of MIG welding. Therefore, it is particularly urgent and important to develop an efficient hot wire TIG welding process.
3.1 Experimental materials
The mother material of the experimental pipe is Q235-A steel, with a thickness of 12mm and an external diameter of 108mm. The chemical composition is shown in Table 1. The tensile strength of Q235-A steel is σb=482MPa, the yield strength is σs=235MPa, and the elongation is δ=26%. The H08Mn2Si welding wire with a diameter of 1.2mm is used. The chemical composition is shown in Table 1. The tensile strength of H08Mn2Si welding wire is σb≥500 MPa, the yield strength is σs≥420MPa, and the elongation is δ≥22%.
Xinfa welding equipment has the characteristics of high quality and low price. For details, please visit: Welding & Cutting Manufacturers - China Welding & Cutting Factory & Suppliers (xinfatools.com)
3.2 Experimental method
The test used the KB370 open-type pipe clamp type pipeline prefabrication high-efficiency hot wire TIG welding system as shown in Figure 1, the PHOENIX-521 multi-function welding power source, and the sharp arc-200 hot wire power source. The hot wire TIG welding process was used, and the joint schematic diagram is shown in Figure 2.
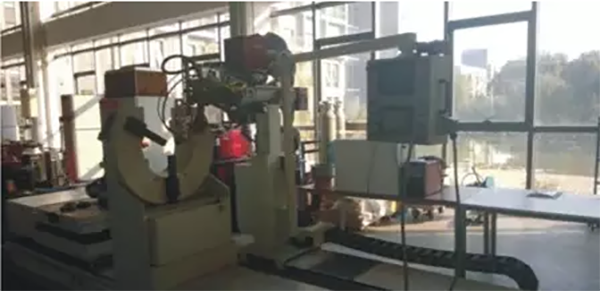
Figure 1 KB370 pipe clamp type high-efficiency hot wire welding system
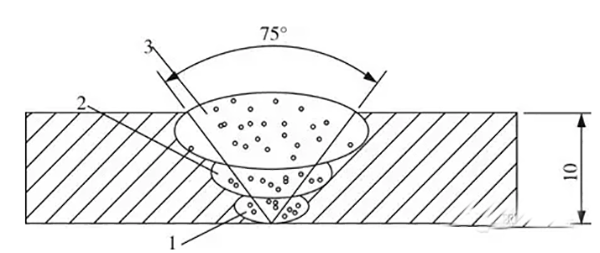
Figure 2 Schematic diagram of the joint
Before welding, the inside and outside of the groove of the pipe test piece are ground and rust-removed, with a range of about 25mm. Before the test welding, the pipe test piece is fixed by spot welding. Three-point spot welding is sufficient. The misalignment is controlled within 1.5mm and there is no gap.
3.3 Experimental results
After the pipe specimens were welded, they were first subjected to X-ray flaw detection, and all passed the I level. Other experiments used macroscopic metallographic, microscopic metallographic and mechanical property tests, as shown in Figures 3, 4, 5, 6 and Table 3, respectively. Figures 3 and 4 clearly show the three-layer weld morphology, the changes in the organizational structure, the small heat-affected zone of the weld, and no pores or cracks. Table 3 shows that the welds were all broken in the parent material area, and the positive bend and back bend met the requirements of GB/T14452-93 standard. As can be seen from Table 4, the following conclusions are drawn:
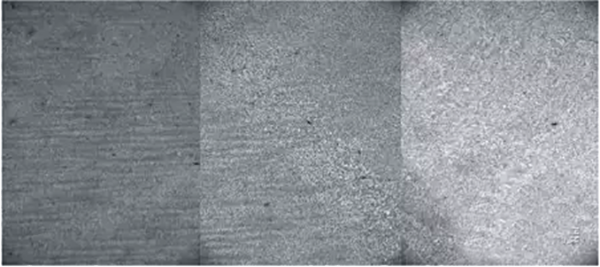
Figure 3 Microstructure of base metal, heat affected zone and weld cross section
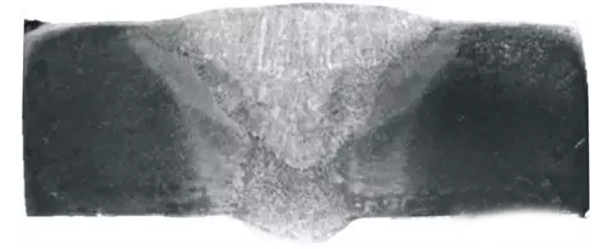
Figure 4 Macroscopic metallographic structure of weld cross section

Figure 5 Tensile test
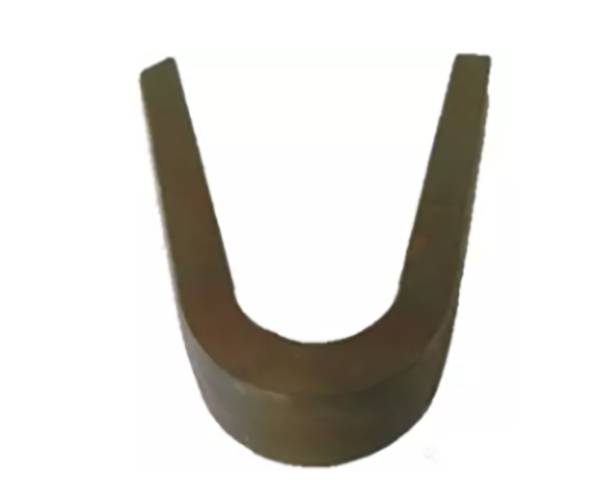
(a) Positive bend
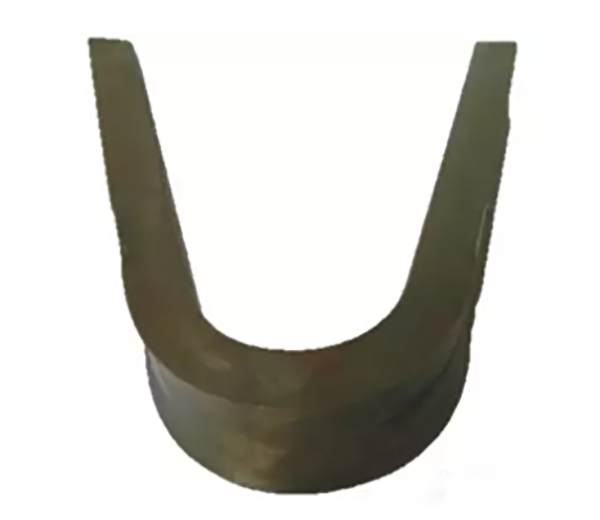
(b)Backbend
High-efficiency hot wire TIG can achieve TIG welding quality and MAG welding speed, but MAG welding has disadvantages such as large spatter, strong arc, large porosity, large line energy, and large grinding amount. Although its deposition efficiency is high, it is obviously not as stable and reliable as TIG welding under high quality requirements. The comprehensive efficiency of high-efficiency hot wire TIG welding is equivalent to or slightly greater than MAG welding;
High-efficiency hot wire TIG welding and traditional cold wire TIG welding have an overall efficiency improvement of 5 to 10 times.
4. Experimental conclusion
4.1 Hot wire TIG welding can obtain a weld with a defect-free surface and good formation;
4.2 The wire feeding speed of hot wire TIG welding reaches 5m/min, up to 6.5m/min, and the melting rate can reach 3.5kg/h, which greatly improves production efficiency;
4.3 The tensile fracture of hot wire TIG welds occurs in the parent material, which improves the joint performance;
4.4 High-efficiency hot wire TIG welding truly achieves the welding quality of TIG welding and the welding speed of MIG welding.
5. Market mature applications and prospects
After nearly two years of market promotion and application, we are currently widely used in marine engineering, gas, instrumentation, petrochemicals, and containers.
The high-efficiency hot wire TIG welding process is not only suitable for carbon steel, but also for alloy steel, stainless steel, duplex steel, nickel-based alloys and other materials (experiments on various materials have shown that, especially in the duplex steel welding process in marine engineering and other industries, high-efficiency hot wire TIG welding does have incomparable advantages). It has broken the monopoly of foreign hot wire TIG welding in China, and its efficiency is 1.5 to 2 times higher than that of foreign hot wires compared with foreign brands.
This technology fills the gap in pipeline prefabrication welding, is an innovative process technology product suitable for China's national conditions, and is a disruptive innovation in the pipeline prefabrication industry. It can completely replace the existing traditional process of TIG primer + MAG filling and covering double composite process, avoiding users from repeatedly purchasing equipment, and is a truly multi-functional and multi-purpose pipeline prefabrication welding system. The welding system with this technology as the core process is currently also applied to the intelligent pipeline prefabrication system, and the market prospects are broad.
Post time: Aug-27-2024