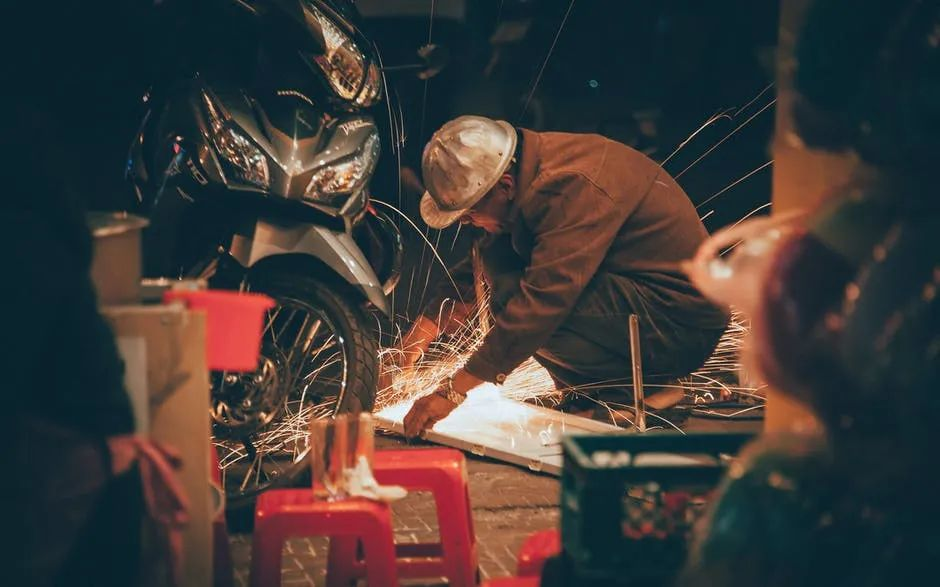
1. Overview
Roll welding is a type of resistance welding. It is a welding method in which the workpieces are assembled to form a lap joint or butt joint, and then placed between two roller electrodes. The roller electrodes press the weldment and rotate, and the power is continuously or intermittently applied to form a continuous weld. Roll welding is widely used in the manufacture of joints that require sealing, and is sometimes used to connect non-sealed sheet metal parts. The thickness of the welded metal material is usually 0.1-2.5 mm.
Bellows are used in valves, mainly for sealing and isolation. In various bellows valves, whether it is a stop valve, a throttle valve, a regulating valve or a pressure reducing valve, the bellows is used as a packing-free sealing isolation element of the valve stem. During the operation of the valve, the bellows and the valve stem are axially displaced and reset together. At the same time, it also withstands the pressure of the fluid and ensures sealing. Compared with packing seal valves, bellows valves have higher reliability and service life. Therefore, bellows valves have been widely used in the fields of nuclear industry, petroleum, chemical industry, medicine, aerospace, etc. In practical applications, bellows are often welded together with other components such as flanges, pipes and valve stems. The bellows are welded by roll welding, which is highly efficient and widely used.
The nuclear vacuum valves produced by our company are used in uranium fluoride environments where the medium is flammable, explosive and radioactive. The bellows are made of 1Cr18Ni9Ti with a thickness of 0.12mm. They are connected to the valve disc and the gland by roll welding. The weld must have reliable sealing performance under a certain pressure. In order to debug and transform the existing roll welding equipment to meet the production requirements, tooling design and process tests were carried out, and ideal results were achieved.
2. Roll welding equipment
The FR-170 capacitor energy storage roll welding machine is used, with an energy storage capacitor capacity of 340μF, a charging voltage adjustment range of 600~1 000V, an electrode pressure adjustment range of 200~800N, and a nominal maximum storage of 170J. The machine uses a zero-enclosed shaping circuit in the circuit, which eliminates the disadvantages of network voltage fluctuations and ensures that the pulse frequency and charging voltage remain stable.
3. Problems with the original process
1. Unstable welding process. During the rolling process, the surface splashes a lot, and the welding slag easily adheres to the roller electrode, which makes it very difficult to use the roller continuously.
2. Poor operability. Because the bellows is elastic, the weld is easy to deviate without proper welding tooling positioning, and the electrode is easy to touch other parts of the bellows, causing sparks and splashes. After a week of welding, the weld ends are not consistent, and the weld sealing does not meet the requirements.
3. Poor weld quality. The weld point indentation is too deep, the surface is overheated, and even partial burn-through occurs. The weld quality formed is poor and cannot meet the requirements of the gas pressure test.
4. Restriction of product cost. The nuclear valve bellows are expensive. If burn-through occurs, the bellows will be scrapped, increasing product costs.
Xinfa welding equipment has the characteristics of high quality and low price. For details, please visit: Welding & Cutting Manufacturers - China Welding & Cutting Factory & Suppliers (xinfatools.com)
4. Analysis of main process parameters
1. Electrode pressure. For rolling welding, the pressure applied by the electrode on the workpiece is an important parameter affecting the quality of the weld. If the electrode pressure is too low, it will cause local surface burn-through, overflow, surface spatter and excessive penetration; if the electrode pressure is too high, the indentation will be too deep, and the deformation and loss of the electrode roller will be accelerated.
2. Welding speed and pulse frequency. For a sealed roll weld, the denser the weld points, the better. The overlap coefficient between weld points is preferably 30%. The change of welding speed and pulse frequency directly affects the change of overlap rate.
3. Charging capacitor and voltage. Changing the charging capacitor or charging voltage changes the energy transmitted to the workpiece during welding. The matching method of different parameters of the two has the difference between strong and weak specifications, and different energy specifications are required for different materials.
4. Roller electrode end face form and size. Commonly used roller electrode forms are F type, SB type, PB type and R type. When the end face size of the roller electrode is not appropriate, it will affect the size of the weld core and the penetration rate, and will also have a certain impact on the welding process.
Since the quality requirements of roll weld joints are mainly reflected in the good sealing and corrosion resistance of the joints, the influence of penetration and overlap rate should be considered when determining the above parameters. In the actual welding process, various parameters affect each other and must be properly coordinated and adjusted to obtain high-quality roll weld joints.
Post time: Sep-12-2024