All defects that can be seen by the naked eye or a low-power magnifying glass and are located on the surface of the weld, such as undercut (undercut), weld nodules, arc pits, surface pores, slag inclusions, surface cracks, unreasonable weld position, etc. are called external defects; while internal pores, slag inclusions, internal cracks, incomplete penetration, and incomplete fusion that must be discovered by destructive tests or special non-destructive testing methods are called internal defects. However, the most common ones are the failure to clean up the slag and spatter after welding and the weld scars.
1. The size of the weld does not meet the requirements of the specification
1.1 Phenomenon: The height of the weld is too large or too small during the inspection; or the width of the weld is too wide or too narrow, and the transition between the weld and the base material is not smooth, the surface is rough, the weld is not neat in the longitudinal and transverse directions, and the concave amount of the weld in the corner weld is too large.
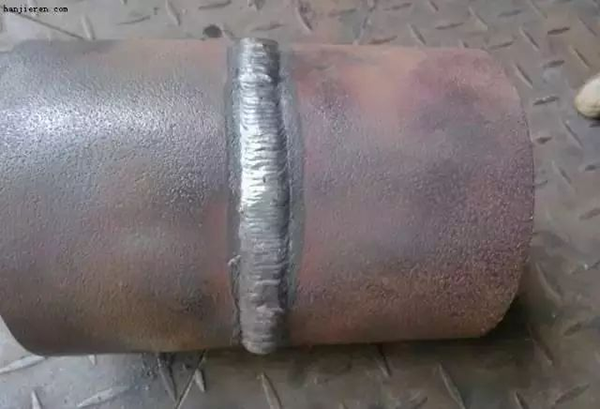
Xinfa welding equipment has the characteristics of high quality and low price. For details, please visit: Welding & Cutting Manufacturers - China Welding & Cutting Factory & Suppliers (xinfatools.com)
1.2 Reasons:
1.2.1 The straightness of the weld groove processing is poor, the angle of the groove is improper or the size of the assembly gap is uneven.
1.2.2 The current is too large during welding, causing the electrode to melt too quickly, making it difficult to control the weld formation. The current is too small, causing the electrode to "stick" when the welding arc is started, resulting in incomplete welding or welding nodules.
1.2.3 The welder's operation is not proficient enough, the rod movement method is improper, such as too fast or too slow, and the electrode angle is incorrect.
1.2.4 In the submerged arc automatic welding process, the welding process parameters are improperly selected.
3. If it is so dangerous, can the baby still sleep on his stomach or side? The answer is: Yes, the adult can watch the baby sleeping on his side or stomach while awake. Proper sleeping on his stomach is very good for the baby. For fear that the baby will choke on milk, the doctor recommends sleeping on the side, so that the baby's whole body can be upward, and the little head can change direction from left to right and upward.
4. Extra bedding also hides danger! In addition to the baby and the seasonal quilt, remove the extra pillows, blankets, stuffed toys, clothes and other debris from the crib. If the baby buries his face in these soft objects, it is likely to cover his mouth and nose, causing difficulty in breathing. The baby's bed does not need to be too soft, and the best choice is a hard baby mattress. Being a parent is not easy, and being a good confinement nanny is even more difficult. Both require persistent learning of scientific parenting. I wish the little babies can have sweet dreams every day, and in the early morning, use the loudest cry or sweet smile to say "good morning" to everyone's parents.
1.3 Prevention and control measures
1.3.1 Process the weld groove according to the design requirements and welding specifications, and try to use mechanical processing to make the groove angle and the straightness of the groove edge meet the requirements, and avoid using artificial gas cutting and manual shoveling to process the groove. When assembling, ensure the uniformity of the weld gap to lay the foundation for ensuring welding quality.
1.3.2 Select appropriate welding process parameters through welding process assessment.
1.3.3 Welders must be certified before they can work. Trained welders have a certain theoretical foundation and operational skills.
1.3.4 For the last layer of multi-layer welds on the welding surface, under the condition of ensuring fusion with the bottom layer, a welding rod with a smaller current than the welding current between each layer and a small diameter (φ2.0mm~3.0mm) should be used for surface welding. The speed of the welding rod should be uniform, rhythmically advancing longitudinally, and making a certain width of lateral swing, so that the weld surface can be neat and beautiful.
2. Undercut (bite meat)
2.1 Phenomenon: The depression or groove melted by the arc during welding is not supplemented by the molten metal and leaves a gap. Too deep undercut will weaken the strength of the weld joint, causing local stress concentration, and cracks will be generated at the undercut after bearing.
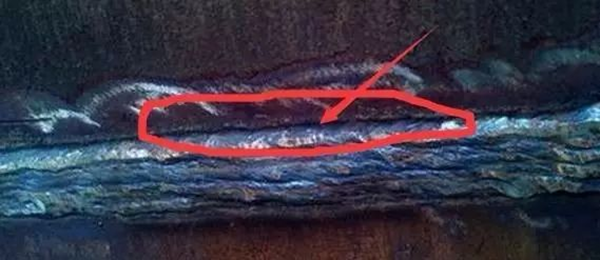
2.2 Reasons:
The main reason is that the welding current is too large, the arc is too long, the electrode angle is not properly controlled, the speed of the electrode is not appropriate, and the length of the electrode left at the end of welding is too short, which leads to the formation of undercut. It is generally a common defect in vertical welding, horizontal welding, and overhead welding.
2.3 Preventive measures
2.3.1 The current should not be too large during welding, the arc should not be too long or too short, and short arc welding should be used as much as possible.
2.3.2 Master the appropriate electrode angle and skilled electrode movement techniques. When the electrode swings to the edge, it should be slightly slower so that the molten electrode metal fills the edge, and it should be slightly faster in the middle.
2.3.3 The depth of the weld undercut should be less than 0.5mm, the length should be less than 10% of the total length of the weld, and the continuous length should be less than 10mm. Once the depth or production exceeds the above tolerance, the defect should be cleaned up, and a smaller diameter and the same brand of electrode should be used. The welding current is slightly larger than normal, and the welding is filled.
3. Cracks
3.1 Phenomenon: During or after welding, metal cracks occur in the welding area. They occur inside or outside the weld, or in the heat-affected zone. According to the location of the cracks, they can be divided into longitudinal cracks, transverse cracks, arc crater cracks, root cracks, etc., which can be divided into hot cracks, cold cracks and reheating cracks.
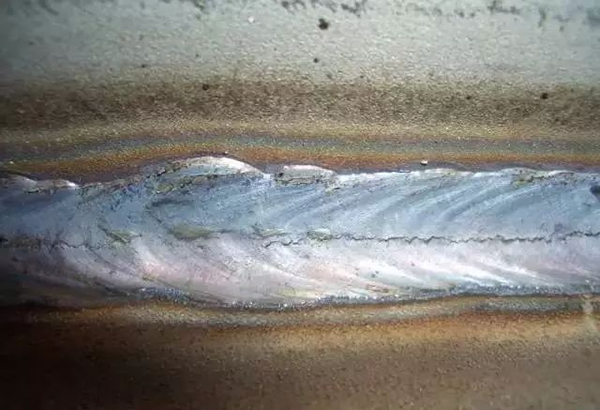
3.2 Causes
3.2.1 Large stress is generated after the heat affected zone of the weld shrinks.
3.2.2 The parent material contains more hardened structures and is prone to cracks after cooling.
3.2.3 There is a relatively high hydrogen concentration in the weld. And other harmful element impurities, etc., are prone to cold and hot cracks.
3.3 Prevention and control measures:
The main solution is to eliminate stress, use welding materials correctly, and improve the operation process.
3.3.1 Pay attention to the groove form of the welding joint to eliminate cracks caused by uneven heating and cooling of the weld due to thermal stress. For example, when welding steel plates of different thicknesses, the thick steel plate must be thinned.
3.3.2 The selection of materials must meet the requirements of the design drawings, strictly control the source of hydrogen, dry the welding rod before use, and carefully clean the oil, moisture and other impurities on the groove.
3.3.3 During welding, select reasonable welding parameters to control the input heat between 800 and 3000℃ cooling temperature to improve the microstructure of the weld and heat-affected zone.
3.3.4 When the welding environment temperature is low and the material is thin, in addition to increasing the operating environment temperature, it should also be preheated before welding. After welding, try to keep the temperature and cool slowly and perform post-weld heat treatment to eliminate delayed cracks caused by residual stress in the weld during the cooling process.
Post time: Jul-26-2024