1. Oxide film:
Aluminum is very easy to oxidize in the air and during welding. The resulting aluminum oxide (Al2O3) has a high melting point, is very stable, and is difficult to remove. It hinders the melting and fusion of the parent material. The oxide film has a high specific gravity and is not easy to float to the surface. It is easy to generate defects such as slag inclusion, incomplete fusion, and incomplete penetration.
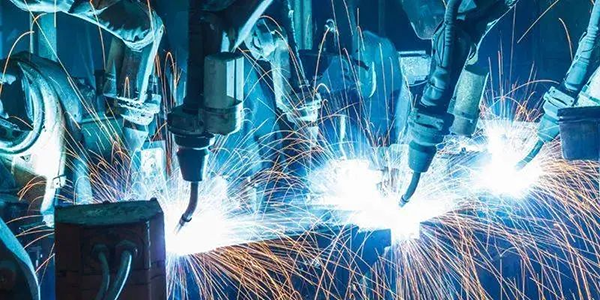
The surface oxide film of aluminum and the absorption of a large amount of moisture can easily cause pores in the weld. Before welding, chemical or mechanical methods should be used to strictly clean the surface and remove the surface oxide film.
Strengthen protection during the welding process to prevent oxidation. When using tungsten inert gas welding, use AC power to remove the oxide film through the "cathode cleaning" effect.
When using gas welding, use a flux that removes the oxide film. When welding thick plates, the welding heat can be increased. For example, the helium arc has a large heat, and helium or argon-helium mixed gas is used for protection, or a large-scale melting electrode gas shielded welding is used. In the case of direct current positive connection, "cathode cleaning" is not required.
2. High thermal conductivity
The thermal conductivity and specific heat capacity of aluminum and aluminum alloys are about twice that of carbon steel and low-alloy steel. The thermal conductivity of aluminum is more than ten times that of austenitic stainless steel.
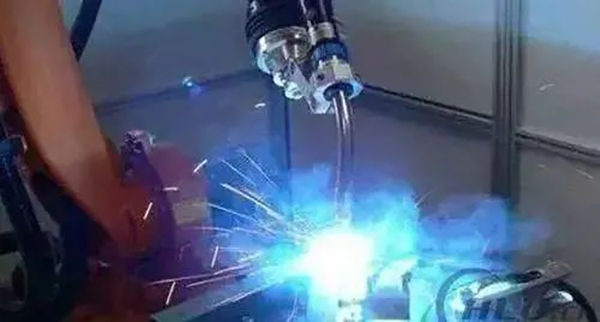
During the welding process, a large amount of heat can be quickly conducted into the base metal. Therefore, when welding aluminum and aluminum alloys, in addition to the energy consumed in the molten metal pool, more heat is also consumed unnecessarily in other parts of the metal. This The consumption of this kind of useless energy is more significant than that of steel welding. In order to obtain high-quality welded joints, energy with concentrated energy and high power should be used as much as possible, and sometimes preheating and other process measures can also be used.
3. Large linear expansion coefficient, easy to deform and produce thermal cracks
The linear expansion coefficient of aluminum and aluminum alloys is approximately twice that of carbon steel and low alloy steel. The volume shrinkage of aluminum during solidification is large, and the deformation and stress of the weldment are large. Therefore, measures need to be taken to prevent welding deformation.
When the aluminum welding molten pool solidifies, it is easy to produce shrinkage cavities, shrinkage porosity, hot cracks and high internal stress.
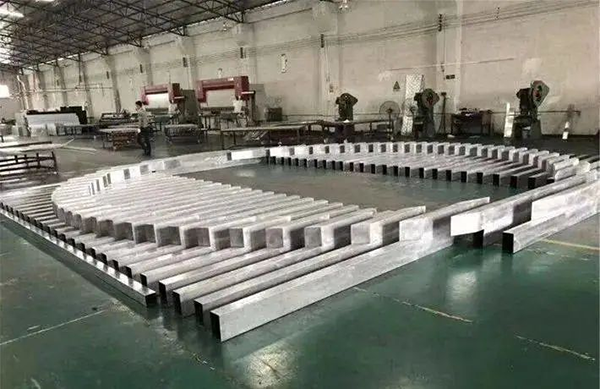
Xinfa welding equipment has the characteristics of high quality and low price. For details, please visit: Welding & Cutting Manufacturers - China Welding & Cutting Factory & Suppliers (xinfatools.com)
Measures can be taken to adjust the composition of the welding wire and the welding process to prevent the occurrence of hot cracks during production. If corrosion resistance permits, aluminum-silicon alloy welding wire can be used to weld aluminum alloys other than aluminum-magnesium alloys. When the aluminum-silicon alloy contains 0.5% silicon, the tendency of hot cracking is greater. As the silicon content increases, the crystallization temperature range of the alloy becomes smaller, the fluidity increases significantly, the shrinkage rate decreases, and the tendency of hot cracking also decreases accordingly.
According to production experience, hot cracking will not occur when the silicon content is 5% to 6%, so using SAlSi strip (silicon content 4.5% to 6%) welding wire will have better crack resistance.
4. Easily dissolve hydrogen
Aluminum and aluminum alloys can dissolve a large amount of hydrogen in the liquid state, but hardly dissolve hydrogen in the solid state. During the solidification and rapid cooling process of the welding pool, hydrogen does not have time to escape, and hydrogen holes are easily formed. The moisture in the arc column atmosphere, the moisture adsorbed by the oxide film on the surface of the welding material and the base metal are all important sources of hydrogen in the weld. Therefore, the source of hydrogen must be strictly controlled to prevent the formation of pores.
5. Joints and heat-affected zones are easily softened
Alloy elements are easy to evaporate and burn, which reduces the performance of the weld.
If the base metal is deformation-strengthened or solid-solution age-strengthened, the welding heat will reduce the strength of the heat-affected zone.
Aluminum has a face-centered cubic lattice and has no allotropes. There is no phase change during heating and cooling. The weld grains tend to become coarse and the grains cannot be refined through phase changes.
Welding method
Almost various welding methods can be used to weld aluminum and aluminum alloys, but aluminum and aluminum alloys have different adaptability to various welding methods, and various welding methods have their own application occasions.
Gas welding and electrode arc welding methods are simple in equipment and easy to operate. Gas welding can be used for repair welding of aluminum sheets and castings that do not require high welding quality. Electrode arc welding can be used for repair welding of aluminum alloy castings.
The inert gas shielded welding (TIG or MIG) method is the most widely used welding method for aluminum and aluminum alloys.
Aluminum and aluminum alloy sheets can be welded by tungsten electrode alternating current argon arc welding or tungsten electrode pulse argon arc welding.
Aluminum and aluminum alloy thick plates can be processed by tungsten helium arc welding, argon-helium mixed tungsten arc welding, gas metal arc welding, and pulse metal arc welding. Gas metal arc welding and pulse gas metal arc welding are increasingly used.
Post time: Jul-25-2024