Aluminum alloy welding is very different from the welding of general carbon steel, stainless steel and other materials. It is easy to produce many defects that other materials do not have, and targeted measures need to be taken to avoid them. Let's take a look at the problems that are easy to occur in aluminum alloy welding and the requirements for welding technology.
Difficulties in welding aluminum alloy materials The thermal conductivity of aluminum alloy materials is 1 to 3 times greater than that of steel, and it is easy to heat up. However, this material is not resistant to high temperatures and has a large coefficient of expansion when heated, which easily causes welding deformation. Moreover, this material is prone to cracks and weld penetration during welding, especially the welding of thin aluminum plates is more difficult.
Xinfa welding equipment has the characteristics of high quality and low price. For details, please visit: Welding & Cutting Manufacturers - China Welding & Cutting Factory & Suppliers (xinfatools.com)
Aluminum alloy welding will produce a certain amount of hydrogen in the molten pool. If these gases are not discharged before the weld is formed, it will cause pores in the weld and affect the quality of the welded parts.
Aluminum is a metal that is easily oxidized, and there is almost no unoxidized aluminum in the air. When the surface of the aluminum alloy is directly exposed to the air, a dense and insoluble aluminum oxide film will form on its surface. The oxide film is extremely wear-resistant and high-temperature resistant, with a melting point of over 2000 degrees Celsius. Once formed, the subsequent processing difficulty will be greatly increased.
Aluminum alloy welding also has problems such as the joint is easy to soften, and the surface tension in the molten state is small and easy to produce defects.
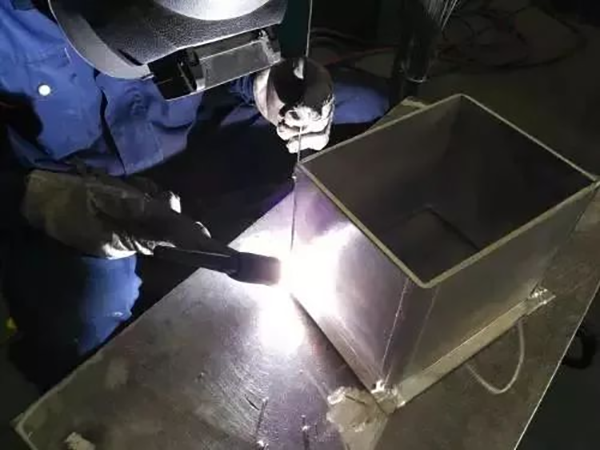
Requirements for aluminum alloy welding process
First of all, from the perspective of welding equipment, if a MIG/MAG welding machine is used, it must have pulse functions such as single pulse or double pulse. The double pulse function has the best effect. Double pulse is the superposition of high-frequency pulse and low-frequency pulse, and low-frequency pulse is used to modulate high-frequency pulse. In this way, the double pulse current is fixed at the frequency of low-frequency pulse to periodically switch between peak current and base current, so that the weld forms regular fish scales.
If you want to change the forming effect of the weld, you can adjust the frequency and peak value of the low-frequency pulse. Adjusting the low-frequency pulse frequency will affect the switching speed between the peak value and base value of the double pulse current, which will change the spacing of the fish scale pattern of the weld. The greater the switching speed, the smaller the spacing of the fish scale pattern. Adjusting the peak value of the low-frequency pulse can change the stirring effect on the molten pool, thereby changing the welding depth. Choosing a suitable peak value has obvious effects on reducing the generation of pores, reducing heat input, preventing expansion and deformation, and improving weld strength.
In addition, from the perspective of the welding process, the following matters should be noted:
First, the surface of the aluminum alloy should be cleaned before welding, and all dust and oil must be removed. Acetone can be used to clean the surface of the aluminum alloy welding point. For thick plate aluminum alloy, it should be cleaned with a wire brush first, and then with acetone.
Second, the welding wire material used should be as close to the parent material as possible. Whether to choose aluminum silicon welding wire or aluminum magnesium welding wire should be determined according to the requirements of the weld. In addition, aluminum magnesium welding wire can only be used to weld aluminum magnesium materials, while aluminum silicon welding wire is relatively more widely used. It can weld aluminum silicon materials and aluminum magnesium materials.
Third, when the thickness of the plate is large, the plate should be preheated in advance, otherwise it is easy to weld through. When closing the arc, a small current should be used to close the arc and fill the pit.
Fourth, when performing tungsten inert gas arc welding, a DC argon arc welding machine should be used, and forward and reverse AC and DC should be used alternately. Forward DC is used to clean the surface oxidation mold of aluminum materials, and reverse DC is used for welding.
Also note that the welding specifications should be set according to the plate thickness and weld requirements; MIG welding should use a special aluminum wire feed wheel and a Teflon wire guide tube, otherwise aluminum chips will be generated; the welding gun cable should not be too long, as aluminum welding wire is soft and a too long welding gun cable will affect wire feeding stability.
Post time: Aug-27-2024